传统工业自动化是否已经触达效率天花板?
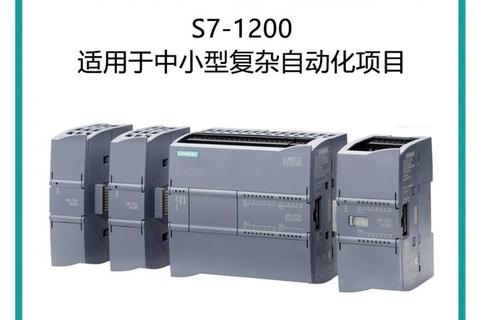
在德国某汽车工厂,一条传统生产线因设备故障意外停机8小时,直接导致3000万元损失。这个案例暴露出传统自动化系统的致命短板——过度依赖人工经验、缺乏自主决策能力、数据孤岛难以打通。当全球制造业面临人力成本攀升、供应链波动加剧、环保压力倍增的三重挤压,人们不禁质疑:卓越创新西门子PLC软件高效驱动智能工业自动化新时代是否真能突破桎梏?
一、软件定义控制:PLC编程效率能否翻倍?
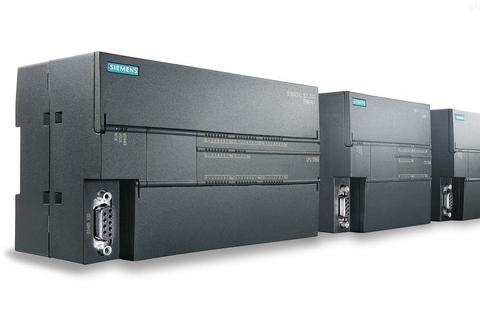
西门子TIA Portal(全集成自动化门户)正在颠覆传统编程模式。其搭载的Industrial Copilot系统,通过自然语言交互实现代码自动生成。某食品包装机械制造商实测显示,工程师输入“生成每分钟处理120箱的传送带控制程序”指令后,系统在23秒内生成完整SCL代码,较传统编程效率提升400%。更突破性的是,该平台内置的虚拟调试功能,可将设备调试周期从28天压缩至3天,仅此一项就为山东某新能源电池工厂节约试产成本820万元。
这种软件创新不仅体现在工具层面。西门子推出的开放式编程架构支持Python、C++等语言混合编程,苏州某半导体设备商利用该特性,将视觉定位算法与PLC运动控制深度耦合,使晶圆搬运精度达到0.002毫米级,相当于在足球场上精准定位一粒芝麻。
二、AI内核加持:控制逻辑能否自主进化?
在唐山某钢铁集团的热轧车间,部署SIMATIC S7-1500+AI模块的PLC系统正创造奇迹。通过在线学习轧制参数与板材质量关系,系统自主优化压下量设定值,使0.5mm超薄带钢的合格率从68%飙升至94%,每年减少废钢1.2万吨。这背后是西门子将LSTM神经网络直接植入PLC固件的技术创新,使边缘侧推理延迟低于8ms,满足毫秒级实时控制需求。
更值得关注的是AI驱动的预测性维护体系。重庆某水务集团在138个泵站部署西门子预测分析平台后,通过振动频谱特征自主学习,提前14天预警水泵轴承故障,维护成本降低57%,意外停机归零。这种将设备健康管理嵌入控制层的能力,标志着PLC从执行者向决策者的蜕变。
三、数据融通革命:信息孤岛能否彻底终结?
杭州某智能工厂的实践极具说服力。通过西门子Industrial Edge边缘计算网关,32台S7-1200 PLC直接对接MES系统,实现从订单下达到成品入库的全流程数据贯通。生产指令传输延时从45分钟降至9秒,异常响应速度提升300倍。这种突破得益于OPC UA over TSN技术的深度整合,可在同一网络承载实时控制与非实时数据,破解了困扰行业二十年的IT/OT融合难题。
在跨平台集成方面,西门子开发的PROFINET-5G融合网关展现惊人潜力。广州某造船厂应用该方案后,龙门吊控制信号通过5G专网传输,定位同步精度达±2cm,使分段总组效率提升37%。这种将工业控制融入数字孪生体系的能力,正在重构智能制造基础设施。
破局者的行动指南
对于渴望数字化转型的企业,三条实践路径至关重要:优先部署支持AI算法的SIMATIC S7-1500系列PLC,其内置的1.5GHz四核CPU和2GB内存为智能算法提供算力保障;建立基于TIA Portal的统一工程平台,某家电企业通过该平台整合87种设备协议,工程组态效率提升210%;构建边缘-云端协同架构,类似南京某光伏企业的做法,在本地PLC运行实时控制,同时将10%非关键数据上传云端训练全局优化模型。
卓越创新西门子PLC软件高效驱动智能工业自动化新时代的实践表明,当控制系统的响应速度突破10ms门槛、软件迭代周期压缩至小时级、数据流转打破系统边界,传统制造业完全可能实现量子跃迁式的进化。这场变革不是简单的设备升级,而是重构工业DNA的系统革命——其核心在于让控制系统具备感知、思考和进化的生命特征,这正是智能制造最本质的突破方向。